Taking a forward-looking view key to fight supply chain shocks
Though the disruption is likely to ease over late 2022, meaningful and material recovery will likely only happen during 2023
image for illustrative purpose
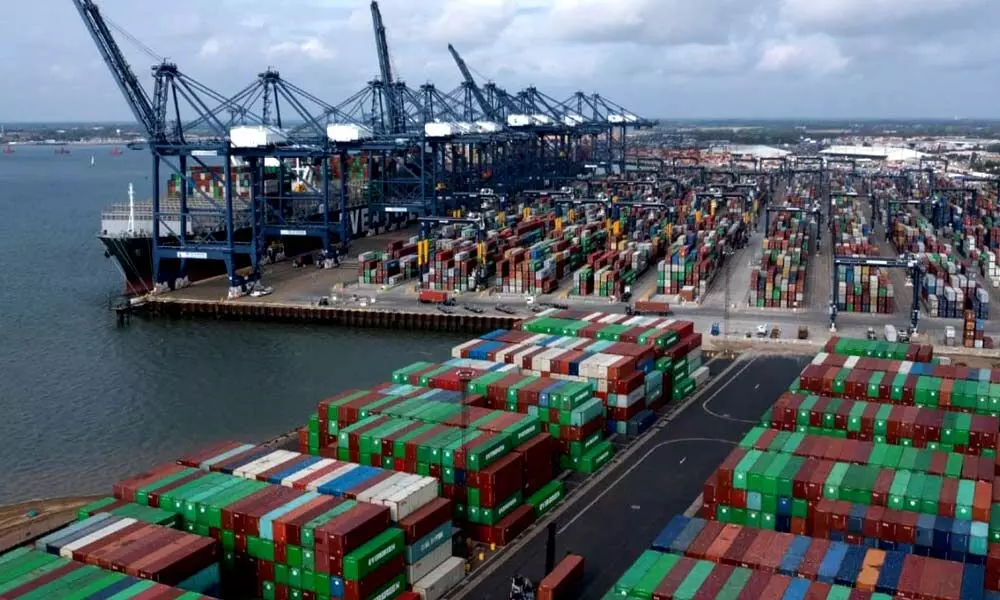
After seeing intermittent disruption to economic activities from the last few Covid waves, we have taken a conservative approach while developing our Base Case forward looking estimates. We expect continued supply chain disruptions until at least Q2 2022. Container freight costs and port congestion have reduced slightly, but still remain at record high levels
The Global supply-chain is a highly complicated system built on interactions between a multitude of state and corporate actors. It is optimized for efficiency, built on the principles of just-in-time and lean production. Over the last few decades, this system has continued to grow in intricacy and scope, becoming more complex and interdependent through multiple recessions and other economic disruptions. However, the unprecedented nature of the pandemic exposed multiple areas of stress in the system. Production levels continue to be marred by issues such as: commodity price inflation, container shortages, port congestion, higher freight cost, and labor shortages among many others.
The impact of supply chain issues in one location or sector were felt across many other geographies and sub-sectors. For instance, pandemic-related disruptions to Outsourced Semiconductor Assembly and Test (OSAT) facilities in South-East Asia exacerbated the semiconductor shortage in the US and led to further cuts to automobile production there. Lower automobile production has in-turn prevented truck transportation companies from expanding their fleet which has led to rising freight rates. The ongoing shortage in the semiconductor industry is the culmination of multiple improbable and successive shocks to its demand and supply. Strong demand in 2020 for consumer electronics such as laptops, computer peripherals, and gaming consoles following the onset of pandemic, prompted consumer electronics manufacturers to increase semiconductor orders. The latter half of 2020 saw a resurgence in automobile demand alongside the gradual re-opening of the economy, which in turn prompted auto-makers to reinstate previously canceled orders. This, along with demand from continuing 5G investment by the telecom sector strained semiconductor industry capacity further.
Meanwhile, supply side came under stress from a series of negative developments led by pandemic-induced lockdowns, as well as other headwinds. Industry capacity was disrupted by the Texas Freeze in February 2021 for example, as well as a fire at Renesas' semiconductor plant in Japan in May. Rising Covid-19 cases in Asia also disrupted critical activities in semiconductor manufacturing such as the Assembly and Test section. It is likely that the shortage may worsen throughout 2022 as lockdowns in China disrupt an already strained chip supply and could even run into 2023, as setting up new manufacturing facilities is a time-consuming process and requires heavy capital investment.
The impact of supply chain issues may differ across sectors, depending on their exposure to global supply networks and their ability to pass on the impact to end customers. Large players are relatively better placed to withstand this disruption due to their diversified suppliers base, sufficient capital back-up and scale benefits, whereas small and medium-sized players have been reeling under pressure due to their concentrated customer and supplier bases. Lenders and banks which are lending to businesses in these sectors, need to be taking a forward-look view to determine how these businesses will fare in the quarters and years ahead. Supply chain challenges such as those outlined could significantly undermine the credit quality of even the most resilient businesses – getting ahead of these with a clear view of the future will not only improve outcomes for the bank, but also the borrower.
After seeing intermittent disruption to economic activities from the last few Covid waves, we have taken a conservative approach while developing our Base Case forward looking estimates. We expect continued supply chain disruptions until at least Q2 2022. Container freight costs and port congestion have reduced slightly, but still remain at record high levels. In addition, Chip manufacturer lead times rose during December'21 after showing a modest dip in November'21. Though the disruption is likely to ease over late 2022, meaningful and material recovery will likely only happen during 2023. However, further downside risk remains, with a continued shortage of raw materials due to emergence of new Covid variant and prolonged labor shortages creating persistent production bottlenecks and straining supply chains.
(The author is a senior director (credit) at OakNorth India)